Key Features
- Web-based tool
- Management of all fieldbus-based data from specification to release
- Development, mapping and maintenance of the communication interfaces of ECUs
- Description of the entire data flow between ECUs and in the ECU itself
- Simple linking with the Sontheim MDT®
- ODX 2.2.0 support
Description
Communication Lifecycle Manager 2.0 (CLCM 2.0)
The CLCM 2.0 of Sontheim Industrie Elektronik GmbH is a central system for the management and creation of diagnostic and communication descriptions of ECUs and entire vehicles. It is a client-server based web application that allows several users to work together on a project. No client installation is required and the server can be accessed from different platforms via the browser. The CLCM 2.0 can be integrated into the existing infrastructure and development process. Thus it can optimally accompany all steps in the development of ECUs and vehicles.
All advantages at a glance:
- High-level overall vehicle structure during the requirement phase
- More precise specification of the ECUs during the implementation phase
- Validation of the described diagnostic and communication interfaces and the mapped bus systems during the test phase
- Provision of generated source code, documentation and diagnostic description after the release
Description of diagnostics and communication
The diagnostic interface of the ECUs is defined in ODX 2.2.0 format. In addition, a description of the communication between the ECUs within the vehicle network can be added. The described diagnostic data serve as a database for source code generation and documentation. The data is stored on a database server, which enables the management of large diagnostic projects. Existing legacy data or data provided by the supplier can be imported at any time. An integrated versioning history displays all changes in the database and allows access to older data statuses for export or display.
The CLCM 2.0 is independent of the protocol and communication system used to describe the diagnostic and communication data. Thus various technologies are supported, including: CAN, K-Line, Ethernet, EtherCAT, J1939, KWP2000onCAN, UDS, CANOpen, UDP, TCP/IP etc.
Code Generator
The CLCM 2.0 has a customizable code generator that can be used to create source code and documentation based on the diagnostic data. The output is fully customizable and can be used by different platforms and programming languages. This allows integration into existing software modules and libraries.
Possible areas of application are:
- Source code for ECU software, diagnostic applications and test environments
- Documentation for the development, production and service departments
The code generator can be integrated into the customer-specific build infrastructure.
Extension API
The CLCM 2.0 has an extension API that allows you to change the default views and create new custom views. Extensions are written in a .NET programming language (e.g. C#) and have access to the complete diagnostic data of the projects.
User Management
- Access to data and files can be restricted for specific user groups and individual users.
- Functions can be switched on and off for specific user groups and individual users.
- Supports authentication via Active Directory
Technical Data
ODX data | Description of all vehicle diagnostic and ECU data in XML Extended to complete image of all communication data Hierarchy models to avoid duplicate data Data abstraction, overwriting and repeated use by reference diagnostic services |
Diagnostic services | Description of diagnostic data such as request/response, param, DataObjectProp, CompuMethod, Unit; Repeated use by references |
Requirements | Data collection of the communication interfaces and the vehicle/machine structure; Protocol-independent data input |
Implementation | Detailed implementation of the interfaces Import function for .dbc and a2I Project view for ODX files, style sheets and test setups Detailed view for comfortable creation of ODX data Table view for editing ODX data even without ODX knowledge |
Test | Execution of communication processes in a test environment Creation of test specifications and protocols Adaptation of the test view via style sheets Comparison with reference values |
Release and diagnosis | Code generator for different platforms and programming languages Diagnostic interface to MDT®; Document management via XSLT, data is converted into .pdf or .doc Firmware release with management and history of different firmware versions |
Server requirements (minimum) | Windows Server 2016; IIS 10.0; SQL Server 2016; CPU: 4 cores; RAM: 6 GB; Memory: 75 GB |
Client requirements (minimum) | Webbrowser (Chrome, Firefox, Edge) |
Related Products
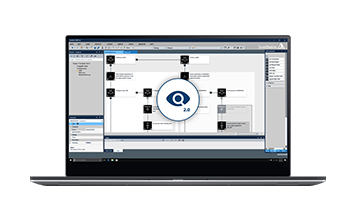
MDT® 2.0
Modular authoring system for the creation of complex diagnostic applications in the automotive sector. Based on ODX and OTX standard and an MCD-3D server.
- ODX support according to ISO 22901-1
- OTX support according to ISO 13209
- MCD-3D Server
- Platform independent
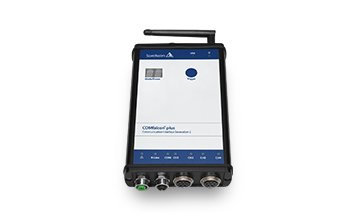
VCIs
High-performance Vehicle Communication Interfaces for development, production and service applications in the automotive sector.
- Up to 6× CAN interface
- WLAN, LAN, Bluetooth, USB, ...
- LIN, RS232, RS485, ...
- With logging function
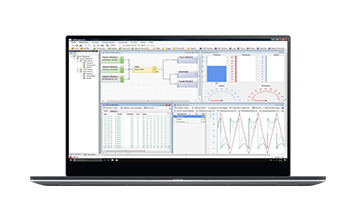
CANexplorer 4
Don’t lose any time during CAN bus diagnostics and benefit from the modular software for acquisition, processing, display and transmission of CAN data.
- Fieldbus analysis tool
- User-defined measurement setups
- Receive, process, send and abstract
- J1939 and CANopen protocol support